Business
OPPO Reno 7: OPPO’s End-to-End Quality Assurance Promise
Published
3 years agoon
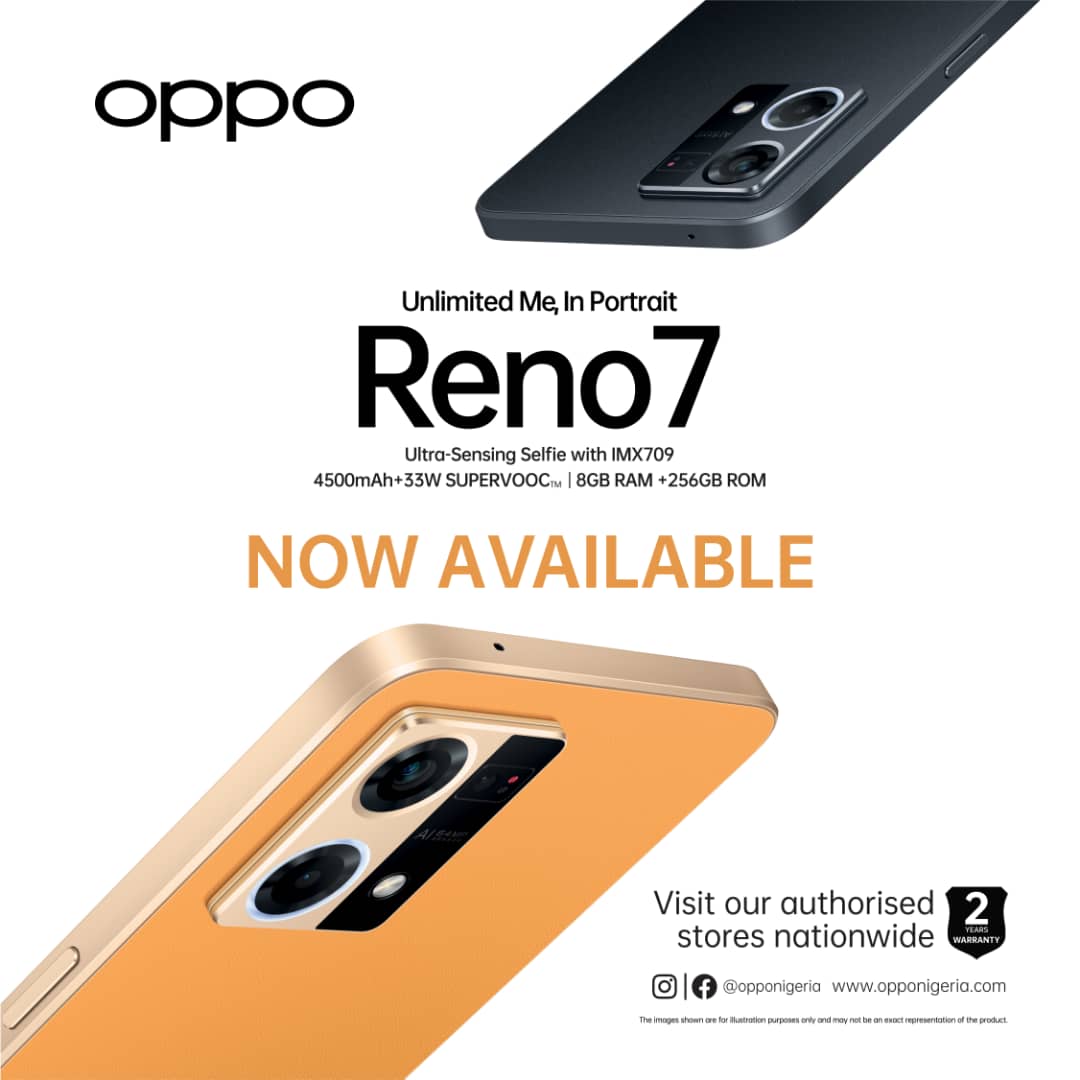
OPPO Reno 7: OPPO’s End-to-End Quality Assurance Promise
Many factors influence a consumer’s decision to purchase a smartphone: the number of smart high-tech features, the phone’s stylish design, or its compact size.
However, if there is one element that can completely turn someone into a loyal fan of a brand, it has to be product quality. With tens of millions of users around the world, OPPO has built its reputation on strict end-to-end quality controls, covering everything from design and manufacturing to quality inspection and after-sales services. These processes are based on a relentless pursuit of attaining the high quality in both product and service, ultimately giving users comprehensive assurance when purchasing a product.
Excellent quality begins with excellent manufacturing
Selecting the world’s top suppliers to guarantee quality from the ground up
OPPO has been actively working with suppliers throughout the industry to create a wide ecosystem of partners. To supply the components that make up the smartphones, OPPO works with many leaders in their respective fields. Take the screen module for example: OPPO partners with Samsung Electronics, Japan Display Inc (JDI), BOE, Tianma Microelectronics, and other manufacturers known for producing top-quality displays and components. OPPO has been working closely with renowned glass suppliers such as Corning and SCHOTT to produce protective screen glass. By partnering with the top suppliers, OPPO is able to manufacture the precisely customized, high-quality components needed to ensure the quality of its end products from the most fundamental level.
Dedicated production lines/factories guarantee the highest standards
To further guarantee the quality of products that come off the production line, OPPO works with its partners to establish dedicated support teams, specialized production lines, and even specialized factories exclusively for OPPO. All components destined for use in OPPO products must be produced in these facilities, which are maintained to the highest standards in the industry. Every worker must undergo OPPO’s extensive pre-work training, including familiarization with OPPO technical documents, and having OPPO technical requirements embedded into the facility’s internal manufacturing processes. Design specifications and quality control procedures are taught to staff, and all production lines are operated by OPPO’s high standard.
Strict production environments also demonstrate OPPO’s precise control over the production line: OPPO requires its suppliers to construct highly intelligent production lines capable of standardized production. Each production line must be strictly certified and monitored, and every item is given a unique ID number to ensure that each tiny procedure can be traced back through the entire production process. When manufacturing smartphone displays for example, all displays are assembled in a Class 1000 dust-free cleanroom that meets more than 270 specifications to ensure standardized production. The production of each component is strictly controlled within fixed specifications to guarantee that every mobile phone provides the same flawless quality.
Rigorous process controls
Even if a smartphone is manufactured according to rigorous production methods, the device needs to be tested before it reaches the market. All OPPO products are required to pass quality and reliability verification on their components, production lines and complete devices. Further to this, independent quality controls are carried out across the entire manufacturing process, including pre- and post-assembly, installation, and completed device stages. If a potential quality risk is detected at any point, OPPO will reject the device, send it back to the manufacturing stage, and solve the underlying issue. Aside from checks performed during manufacturing, engineers and technical experts also conduct five rounds of comprehensive quality assessments and reviews. These include evaluations during products planning, design, development, and verification. If a smartphone fails during any round, it is not allowed onto the market.
Innovation based on assured quality
As a famous saying at OPPO goes “product quality comes from good design”. Part of the role of OPPO’s R&D personnel involves taking specific user needs and transforming them into higher quality user experiences through tailored product design. Good product design is more than just appearances – it requires guaranteeing that every feature and every aspect of the device delivers on its promise to users.
Dedicated designs make every promise a reality
Production feasibility needs to be taken into account from the very outset if design innovations are to perform as intended. OPPO product designers therefore need to create clear and detailed product blueprints with enough information for factory workers to understand and follow accurately. This requires product designers to think ahead during the product planning stage to consider problems that might be encountered during production and manufacturing, and then come up with detailed solutions before the designs are put into production.
Practical and durable process innovation
Not every imaginative design idea makes its way onto the smartphones. OPPO takes a very cautious approach to commercializing new designs. A novel design requires hundreds, or even thousands of trials, including material selection, testing of the manufacturing process, quality verification, or months of technical testing before it is brought to consumers on a finished smartphone.
Take the new Reno7 Sunset Orange for example. In order to give the back cover of the phone an expressive textured effect that also feels smooth in the user’s hand, OPPO designers examined thousands of different textures. Eventually, the team of designers narrowed down thousands of potential materials to just six options. Further market research on these six textures finally led to the selection of a lychee grain leather texture, chosen for its suitable thickness and natural, skin-friendly touch.
The designers then came across another new challenge when attempting to bring the exact textural effect to the back cover of the smartphone. To solve this, OPPO devised its own innovative Fiberglass-Leather made up of a synthetic leather material and a plate combined into one integrated piece designed to perfectly fit the shape of the phone. Compared with traditional leather covering processes, the Fiberglass-Leather design introduces a “frameless battery cover”, meaning that no plastic mid-frame support is required. This new leather and fiberglass construction results in a lighter, thinner, and more integrated back cover without compromising on practicality and durability.
Such innovations in design require further exploration in new applications of technologies and materials. To bring the appearance of high-quality leather to the Reno7 series, OPPO tested and modified ten different polyurethane materials and six bridging layers, and made five modifications to the glass fiber epoxy resin. To ensure the material could withstand up to 100°C heat and 1.5mPa of pressure for 4 hours during the manufacturing process, OPPO engineers strengthened the temperature resistance of the leather polyurethane material to 190°C and increase its tensile strength to 20mPa, ensuring that the material’s appearance did not warp during production. Together, these steps make it possible for the leather back cover to be mass produced at the desired level of quality.
Stringent testing of every detail
After the design and manufacture stages, more testing is required to fully guarantee that the finished product meets OPPO’s high standards before it arrives on the market.
Global test centers provide professional quality assessment
OPPO has established quality testing centers in China, India, and Indonesia, a professional quality team made up of hundreds of engineers and technical experts. OPPO’s quality laboratory has even been accredited by authorities such as the China National Accreditation Service for Conformity Assessment. In these quality testing centers, products need to pass more than 130 ultra-rigorous reliability tests, 320 experimental tests, and 6 major tests before they are ready for the next stage.
Comprehensive general testing goes beyond industry standards
OPPO products are only deemed fit for consumers if they have successfully passed a series of rigorous quality tests. These cover all day-to-day usage scenarios that the phone is likely to come across, including waterproofing tests, temperature and humidity tests, drop tests, RF tests, audio tests, radiation tests, battery tests, button pressing tests, plugging tests, twisting tests, light aging tests, cosmetics tests, extreme environment tests, clothing tests, and many more. To guarantee the same high quality for users around the world, some of these tests have much higher requirements than the industry average. For example, the drop test, which simulates a typical free-fall scenario from various heights, was set at a height of 1 meter for OPPO phones against an industry average of 0.8 meters. These comprehensive, demanding tests ensure OPPO devices can be used as expected in both regular and extreme environments.
Specific tests for special quality control
Apart from tests designed to ensure regular performance and functionality, OPPO also conducts specific tests to ensure the durability and practicality of innovative features or design elements. For instance, the Fiberglass-Leather on Reno7 Sunset Orange has been subjected to extreme lab tests involving rubbing the material with an alcohol-soaked pad, a rubber eraser, and a denim swatch over 5,000, 10,000, and 200,000 times respectively. By simulating daily wear and tear in this way, OPPO ensure that its innovative designs are durable and resistant enough to meet its high standards.
This same insistence on excellence can also be found in the high level of quality control around design details. The Orbit Light, which surrounds or embedded in the camera module on certain smartphone models, OPPO conducted over twenty uniform light scheme adjustments, thousands of uniform light detection tests, and other special tests. In the standard test environment (25°C, 60% humidity, 10mAh), the lifespan of the Orbit Light was shown to reach over 50,000 hours. Through these special quality control tests, OPPO can ensure that even the smallest of innovations deliver a reliable, fault-free experience.
Quality assurance from start to finish
To deal with issues caused by minor accidents during daily use, OPPO has established professional and friendly after-sales teams worldwide to provide services to every OPPO user, making up the final link in OPPO’s end-to-end quality assurance.
Following the opening of the first service center in Lagos Nigeria, OPPO began to rapidly rollout more centers nationwide. As of 2021, OPPO has established more than after-sales centers in Nigeria and regions such as Lagos, Abuja, Porthacourt, Ibadan, together, more than 100 customer service representatives work in these service centers.
Through these after-sales service centers, OPPO has built up a high-quality service model based on its Care & Reach philosophy. Through Care & Reach, OPPO brings customers industry-leading after-sales services based on three core values: Friendly Service, Professional Service, and Inspiring Service. For example, OPPO has introduced “1 Hour Flash Fix”and “Send-in Repair services”, making it possible for users to have their smartphones repaired quickly and efficiently. At the same time, these user-friendly services enable OPPO technical engineers to improve their troubleshooting skills and efficiency, helping them to provide faster, more convenient, and more professional services at all times.
Product quality can be very difficult to prove when it comes to complex devices such as smartphones. It is not until something goes wrong that an individual starts to question its quality. Therefore, OPPO bases its quality standard not on the results of factory testing but on direct feedback from the market. This includes things such as the maintenance rate for a certain device, and the product withdrawal rate.
Thanks to OPPO’s high quality requirements and rigorous quality control, failure rates for OPPO products available on the market are far below those of the industry average. For example, the failure rate from water damage is far lower than the industry average; products are also less likely to result in severe damage after being dropped and are more reliable when used in very humid climates or other extreme environments. Building upon this success, OPPO will continue to make quality a cornerstone of its commitment to consumers, bringing users reliable products and high-quality services through its end-to-end quality assurance program.
Related
Sahara weekly online is published by First Sahara weekly international. contact saharaweekly@yahoo.com

Business
Tinubu’s Economic Agenda in Crisis: North-South Divide Strikes Again
Published
7 hours agoon
April 22, 2025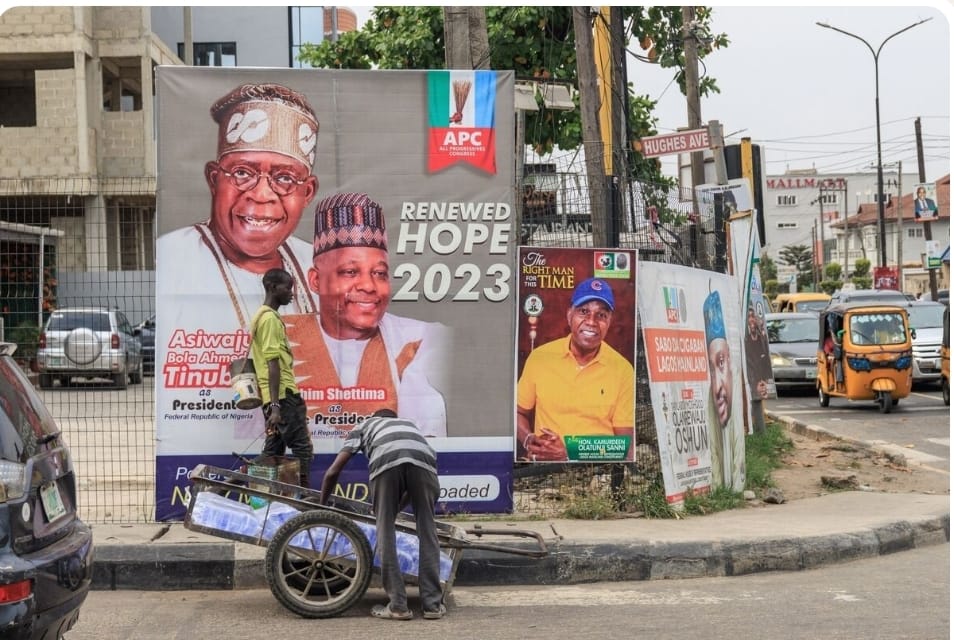
Tinubu’s Economic Agenda in Crisis: North-South Divide Strikes Again
By George Omagbemi Sylvester
President Bola Ahmed Tinubu, elected in 2023 on the wings of political calculation and elite manipulation, has now found himself caught in the snare of Nigeria’s enduring historical curse: the north-south divide. His ambitious economic reform agenda, intended to liberalize the economy, remove structural inefficiencies, and reduce government expenditure—has hit a legislative wall. But this isn’t just about policy. This is about power, patronage, and the ancient scars of a fractured federation.
The rejection of critical aspects of Tinubu’s economic proposals by lawmakers is a stinging rebuke, not only to his administration but to the very idea that Nigeria can be reformed from the top down without confronting its structural imbalances. In many ways, Tinubu’s presidency is now facing the same nightmare that has haunted every Nigerian leader since independence: how do you govern a country that was never truly united?
The Crumbling Reform Agenda
At the center of the storm is Tinubu’s proposal to centralize and streamline federal subsidies and remove what he termed “wasteful duplication of agencies.” This was meant to continue the subsidy removal narrative started in June 2023, and reduce fiscal leakage. However, the backlash, particularly from legislators representing the northern states, was swift and coordinated.
The northern bloc, comprising lawmakers from Kano, Katsina, Kebbi, Sokoto, and Borno, objected on the grounds that Tinubu’s proposals disproportionately affect their regions, where federal allocation remains a critical lifeline in the absence of strong internally generated revenue. But critics argue this is a strategic form of sabotage, aimed at retaining an unsustainable status quo that prioritizes political patronage over national progress.
As Prof. Wale Adebanwi of Oxford University has argued, “Nigeria’s northern elite have historically benefited from the spoils of a rentier state, with oil wealth redistributed without the burden of productive contribution. Any move to reverse this equation is seen as existential.”
Tinubu, a southerner from Lagos, with strong Christian support from the Southwest and Southeast, is now facing the very brick wall that has impeded reforms since the First Republic. His own political survival now depends on how much compromise he’s willing to make—or whether he can break the mold entirely.
A Century-Old Fracture
The rejection of Tinubu’s reforms by northern lawmakers is not new. It is deeply rooted in a century-old tension embedded in the structure of the Nigerian state. The 1914 amalgamation, engineered by British colonialists, fused two vastly different regions, the industrializing, Western-educated Christian south and the feudal, Islamic north, into one artificial political entity.
From independence in 1960, this contradiction has remained unresolved. “Nigeria was created not to function as a cohesive nation, but as an economic convenience for its colonial masters,” noted historian Max Siollun. “What we’re seeing is the consequence of a nation built on convenience rather than consensus.”
The economic priorities of the north and south remain deeply divergent. While the south boasts ports, oil revenue, industries, and a growing tech sector, the north has remained largely agrarian, dependent on federal allocations and political appointments. Any attempt to tamper with this redistribution—whether via subsidy removal or cuts in federal spending, provokes immediate resistance.
Reform vs. Redistribution
Tinubu’s administration promised reforms: subsidy removal, tax reform, and investment in critical infrastructure. But all reforms require sacrifices, and those sacrifices must be nationally distributed to succeed. What Tinubu is discovering, painfully, is that reforms without inclusive buy-in are dead on arrival.
Economist Dr. Obiageli Ezekwesili captured the challenge succinctly: “Nigeria’s political economy is structured around the sharing of oil rents, not the creation of wealth. Any attempt to disrupt this structure will provoke fierce opposition from those who depend on the current dysfunction for survival.”
Indeed, the loudest resistance to Tinubu’s reforms has come not from the opposition PDP or Labour Party, but from within his own APC, particularly from northern senators and representatives who feel alienated by the president’s southern-centric economic vision.
The Ghost of Buhari
Many Nigerians are now drawing comparisons between Tinubu’s presidency and that of his predecessor, Muhammadu Buhari, a northern Muslim who governed with overwhelming support from the north. Buhari’s policies favored heavy spending, a bloated civil service, and minimal economic restructuring, a model that created illusions of stability while deepening the economic rot.
“Buhari governed like a tribal chief, rewarding loyalty over competence, and expanding a culture of dependency,” said Prof. Kingsley Moghalu, former Deputy Governor of the Central Bank. “Tinubu’s efforts to break away from that legacy will require courage, strategy, and above all, an appeal to national interest.”
But appealing to national interest in Nigeria is easier said than done. The political class thrives on division. The north fears marginalization, the south resents over-centralization, and the middle belt remains trapped in identity crises. Tinubu, in failing to build a coalition around his reforms, is now paying the price of elite disunity.
The Danger of Ethno-Political Paralysis
The rejection of Tinubu’s agenda is not just a political problem, it is an economic time bomb. Nigeria is drowning in debt, with over 90% of its revenue now going to debt servicing. Inflation is running rampant, the naira has crashed, and unemployment remains alarmingly high. The country cannot afford to maintain the current level of government spending without reform.
But if every economic policy must first pass the tribal test, then reform is doomed. “A nation that filters every economic decision through the lens of ethnicity is a nation marching toward collapse,” warned Nobel Laureate Wole Soyinka. “If Nigeria cannot rise above its primordial divisions, it cannot survive the 21st century.”
What Next for Tinubu?
Tinubu’s next steps are critical. Will he revise his reforms to appease northern lawmakers and keep the political peace? Or will he double down, use executive power, and mobilize the Nigerian people behind a populist push for structural change?
There is a middle path, dialogue, renegotiation of the federal structure, and regional empowerment. Many have called for fiscal federalism, where regions generate and control their own revenues, sending only a fraction to the center. This model, already practiced in countries like Canada and the United States, could reduce the perennial tension around federal allocation.
Political economist Ayo Teriba suggests, “Nigeria must move away from revenue-sharing to revenue-generation. That shift requires not just policy but a new national consensus, and that is where Tinubu must lead.”
In conclusion: Lead or Collapse
President Tinubu is at a crossroads. He can continue playing the dangerous game of balancing regional interests with national imperatives, or he can rise above the tribal chessboard and lead with boldness. The north-south divide is not just a historical relic, it is a living cancer that must be addressed through structural reform, not rhetorical appeasement.
The economic reform agenda is not a southern agenda. It is a Nigerian necessity. If lawmakers continue to sabotage reform because it threatens their regional comfort zones, then the entire nation will suffer. As the saying goes, “A house divided against itself cannot stand.”
In the end, Tinubu must decide: will he be a president of compromise, or a reformer of consequence?
Related
Business
Adron Homes Celebrate Easter, Offers Up to 30% Discount and Flexible Payment Plan
Published
2 days agoon
April 20, 2025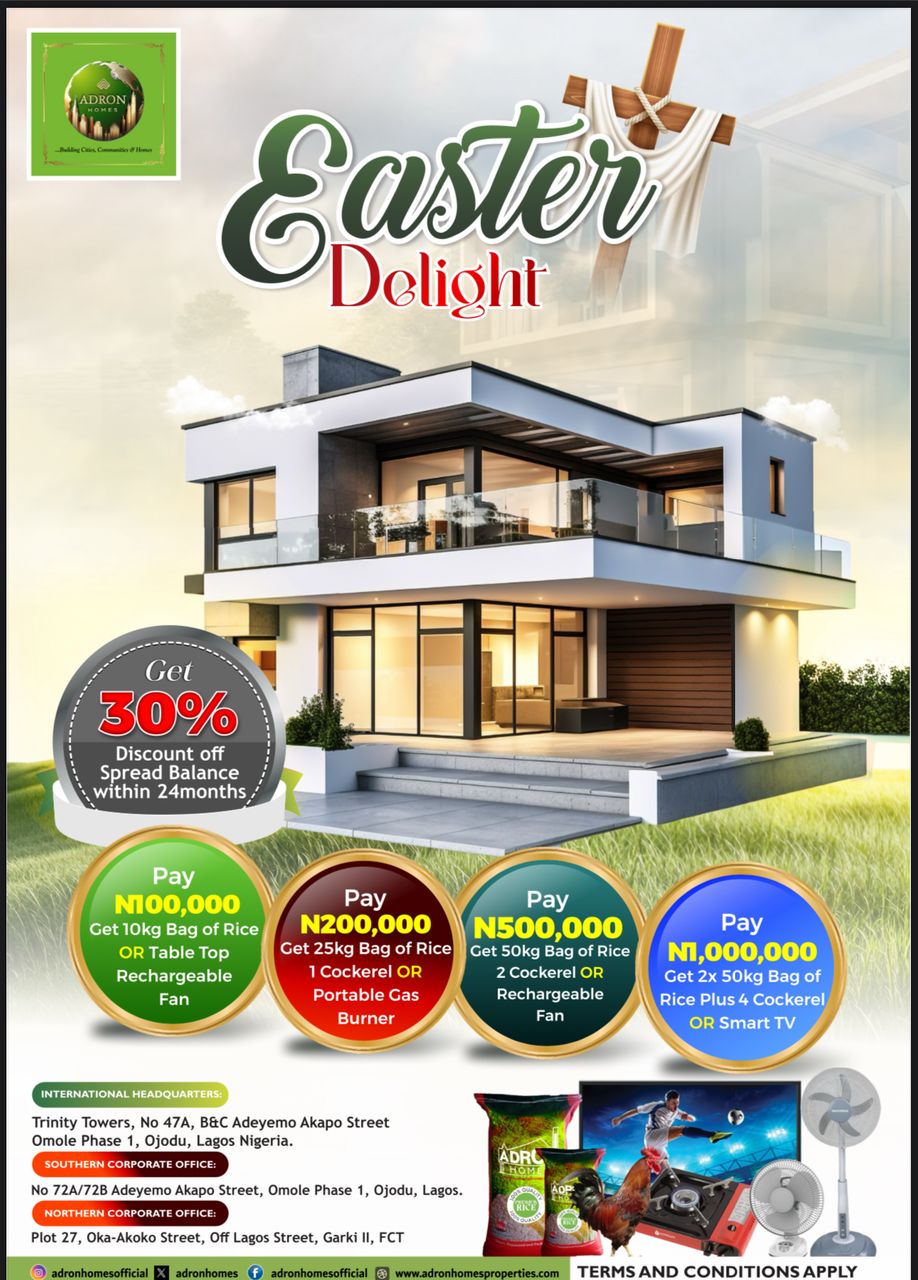
Adron Homes Celebrate Easter, Offers Up to 30% Discount and Flexible Payment Plan
Adron Homes and Properties, Nigeria’s foremost real estate company, joins Christians nationwide and beyond in celebrating Jesus Christ’s resurrection this Easter season.
Easter, a time of reflection, sacrifice, and joyful renewal, reminds us of the triumph of life over death, hope over despair, and love over fear. It is a season that inspires faith, unity, and the promise of new beginnings for individuals, families, and communities alike.
In a statement released by the company, Adron Homes expressed heartfelt appreciation to its Christian clients and stakeholders for their continued trust and loyalty.
“Easter is a season that embodies the spirit of renewal and grace. At Adron Homes, we are inspired by the hope it brings and the values it represents. We remain committed to building not just houses, but vibrant communities where families can thrive, grow, and create lasting memories,” the company stated.
As part of the celebration, Adron Homes announced that its Easter Delight Promo is still ongoing. The promo offers up to 30% discount on all properties nationwide, along with a flexible payment plan of up to 24 months, making homeownership more accessible and convenient than ever.
Even more exciting, subscribers during the Easter promo stand a chance to win fantastic gifts, including bags of rice, whole chickens, rechargeable fans, gas burners, smart TVs, and many more household essentials — adding extra joy to the season of giving.
With estates strategically located in Lekki-Epe, Badagry, Shimawa, Ibadan, Abeokuta, Ede (Osun), Osunjele, Ilisan, Jos, Sagamu, Ado-Ekiti, Atan-Ota, Ikorodu, Papalanto, Ijebu-Ode, Abuja, Nasarawa, Niger, and more, Adron Homes continue to bridge the housing gap by offering luxurious yet affordable properties in fast-growing areas across the country.
Through its unwavering commitment to excellence, Adron Homes ensures every Nigerian has access to premium real estate and the opportunity to achieve their dream of homeownership.
As Christians mark this sacred occasion with loved ones, Adron Homes wishes every Nigerian peace, joy, and the grace of new beginnings.
Related
Business
Harmony Gardens, FG Launch Renewed Hope Estate for Nigerians Abroad
Published
4 days agoon
April 18, 2025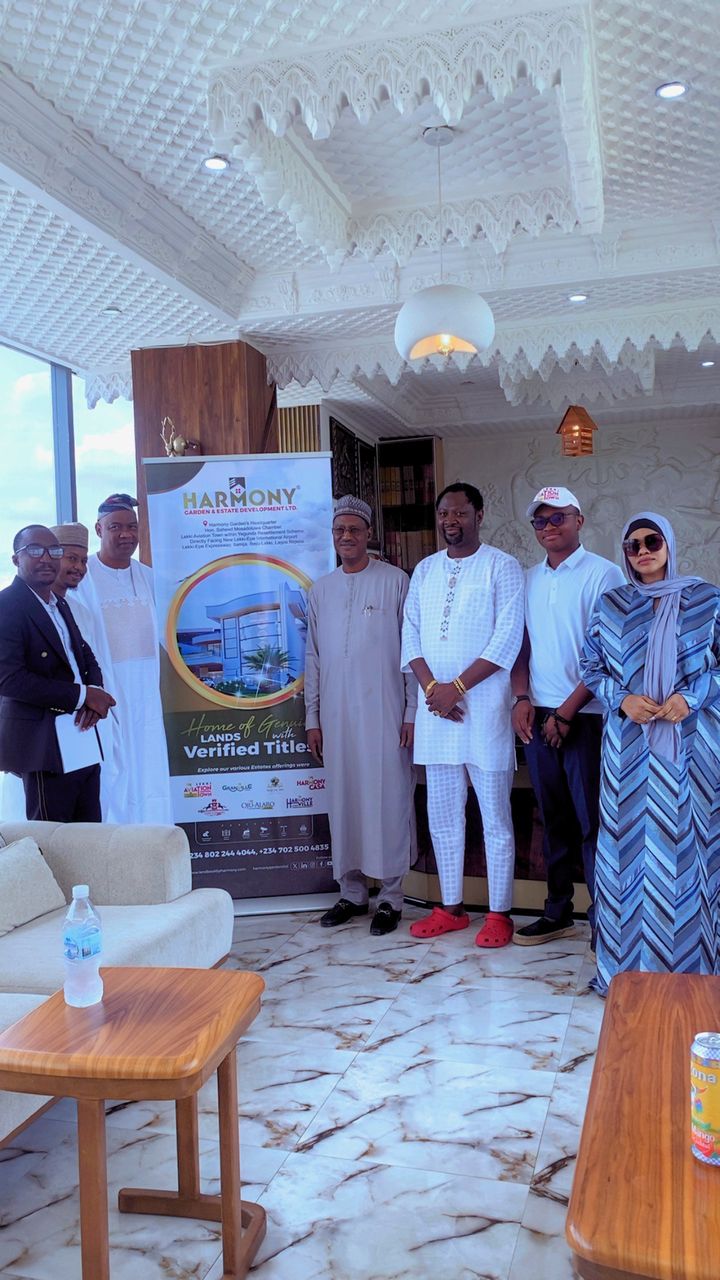
Harmony Gardens, FG Launch Renewed Hope Estate for Nigerians Abroad
Top Lagos-based real estate powerhouse, Harmony Gardens & Estate Development Ltd, is once again making waves, this time through a landmark partnership with the Federal Government of Nigeria to deliver 1,000 modern duplexes at Lekki Aviation Town, directly opposite the proposed Lekki International Airport.
The project, part of President Bola Ahmed Tinubu’s Renewed Hope Agenda, is targeted at middle-income Nigerians in the diaspora seeking to invest in sustainable, high-quality housing back home. It is being financed by the Federal Mortgage Bank of Nigeria (FMBN) and reflects the government’s commitment to easing access to homeownership.
President Tinubu is set to perform the official groundbreaking on May 29, 2025, signaling not just political will but also strategic action toward diaspora inclusion and infrastructure expansion.
Speaking on the initiative, Harmony Gardens Chairman, Mogaji Wole Arisekola, confirmed a whopping ₦106 billion investment into the FGN Harmony Partnership. The company’s innovative Executive Managing Director, Hon. (Dr.) Abdullahi Saheed Mosadoluwa, widely known as The Lagos Landlord is rolling out a game-changing Ibile Traditional Mortgage Scheme. The plan offers Nigerians at home and abroad the ability to rent-to-own homes on a single-digit annual interest rate for up to 20 years.
The Renewed Hope Estate will boast modern infrastructure, green areas, high-grade finishes, security systems, and effective drainage, setting a new standard for residential developments in Lagos. It will also provide over 5,000 direct and indirect jobs, boosting the construction and logistics sectors significantly.
Harmony Gardens has continued to solidify its reputation as a premium developer, currently overseeing seven prestigious estates, including GranVille Estate, The Parliament, Majestic Bay, Harmony Casa, and the flagship Lekki Aviation Town, collectively known as the Seven Citadel of Joy.
As the federal government collaborates with developers and international consultants to ensure timely delivery and top-tier quality, Harmony Gardens is once again demonstrating why it remains a pillar of excellence in Nigeria’s real estate industry.
Related
Trending
-
Business6 months ago
Comprehensive Media Audit Shows Flutterwave, MTN Nigeria, and Bolt Outpacing Competitors in Media Engagement
-
celebrity radar - gossips7 months ago
How Deji Adeyanju Secured The Release Of Speed Darlington
-
Politics7 months ago
My best is yet to come’ As Ambassador Adesina ‘Lanre Ogunsola affirmed at the APC APEX body, Obafemi Owode Local Government
-
Entertainment4 months ago
Aliu Gafar delivers stellar performance as Esusu in Femi Adebayo’s Seven Doors